This article will introduce the crystallized glass processing method from the following aspects
- How to choose equipment with sound mechanical performance?
- What should be paid attention to when cutting crystallized glass stone with bridge cutting equipment?
- What should be paid attention to when processing the edge of the Nano glass slab?
- Crystallized glass drilling
- Crystallized glass for stair
How to choose equipment with sound mechanical performance?
Choose equipment with sound mechanical performance, such as a saw with a sharp edge and a thickness ranging from 1.5 mm to 2.2 mm. Before every cutting, be sure to grind the edge of the saw blade with firebrick for a duration of not less than 15 minutes. The diameter of the saw blades chosen ranges from 350 mm to 400 mm (a special saw blade is preferable).
What should be paid attention to when cutting crystallized glass stone with bridge cutting equipment?
Pay attention to cutting speed during cutting slab and normal speed shall be 2.5 m/min to 5 m/min; when the blade is cutting into and taking off from the slab, keep a low speed, to avoid slab edge or border being broken; the rotate speed of cutter and main blade shall be around 2500 rmp. Higher RPM would have better cutting efficiency.
When cutting Crystallized Glass tiles which have a dimension of 1000 x 1000 mm, be sure the Crystallized Glass slab is steady on the cutting machine. Swaying of the slab would cause damage when cutting.
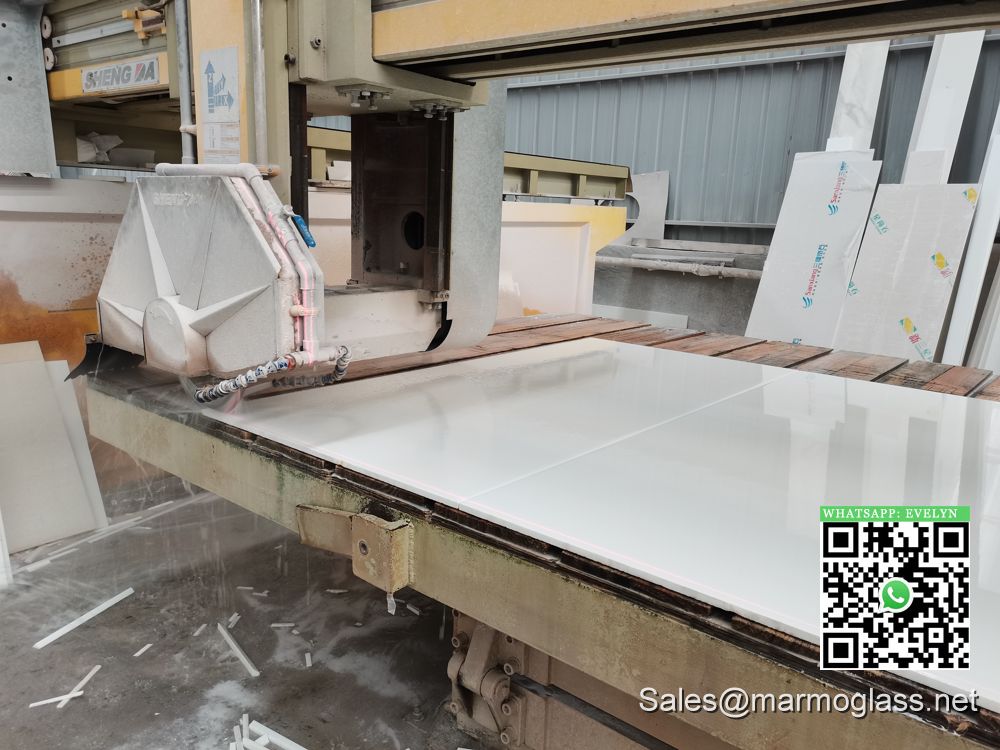
Nano glass Infrared bridge cut
What should be paid attention to when processing the edge of the Nano glass slab?
The well-cut crystallized glass slabs shall be separated by pearl cotton in the deposit to avoid being damaged.
The crystallized glass tiles shall be processed by using the machining techniques of border grinding and edge rounding, for which a glass straight border grinding machine may be used. During slab grinding, please note the force that each grinding head bears, and the grinding/cutting volume of each emery wheel shall not be over 1 mm. Keep the main strap of grinding machine being in accordance with slab-in strap horizontal, otherwise, uneven will occur to the slab. A grinding wheel shall be used for the edge and border polishing. If not available, a portable water grinder may be used.
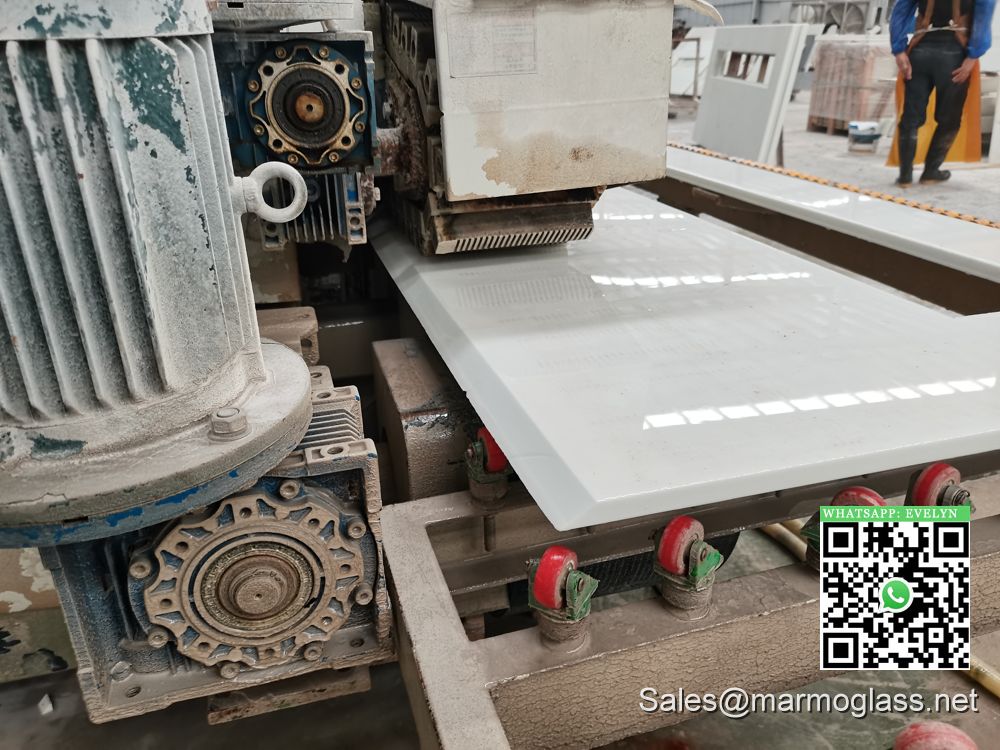
Nano glass edge processing
Crystallized glass drilling
In heteromorphic table machine or water basin hole drilling, please choose Diameter 35 glass aiguilles and mark the outline of the hole, then drill several small holes around the hole with stone materials or glass dedicated aiguilles; be noted to drill holes at four corners with cooling water. At the same time, the cutting blade shall be well ground on the firebrick for operation; operation gently in cutting; I the slabs can not be wholly separated in one cut, please cut with several com-and-goes and cooling water being used. Dry-grinding shall be avoided to prevent the slab from breaking.
Crystallized glass for column cladding
In arc border rounding, please mark it first and form the outline with a hand grinder, then polish it with a portable water grinder, with the operation method the same as that of the other stone materials. What shall be noted is that dry grinding is to be avoided and water cooling is to be applied in polishing. In border thickening, both surfaces to be joined shall be roughed with grinding, first cutting the line out from the cutter, then grinding with the above method, and the optimal effect will be obtained.
For 45-degree back beveling, the gradient of the main blade on the cutter shall be adjusted by hand, the working table shall be cleaned, and then the positioning slab adjusted. It is better that a layer of rubber be placed on the working table before putting the China Marmoglass slab on it to avoid the polished surface being scratched; prior to machining, the saw shall be ground and the water level checked, and keep a slow speed in operation.
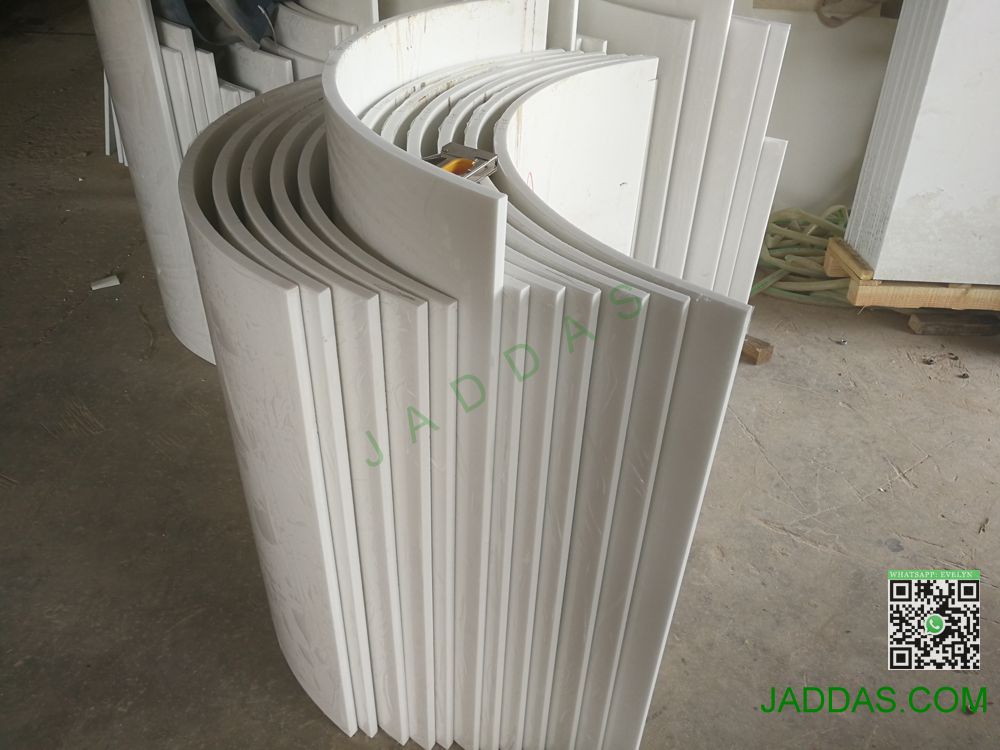
Nanoglass Columns
Crystallized glass for stair
In stair panel machining and skid-proof groves forming, the stair slabs shall be thicknessed, edge-rounded, and cut at a 45-degree angle, with the operations illustrated in items 6 and 7 being followed. Pay attention to the border of the heteromophic slab. It is better that back-cutting be used for the border cutting and that we follow the client’s requirements for skid-proof groove forming. A hand-turned border cutter shall be used during groove forming, and groove width and depth shall be well adjusted, and a saw blade (in 2.4 mm thickness) shall be chosen according to the width; generally, two saw blades shall be installed based on the groove sizes; the formed groove shall be polished with the portable water grinder.
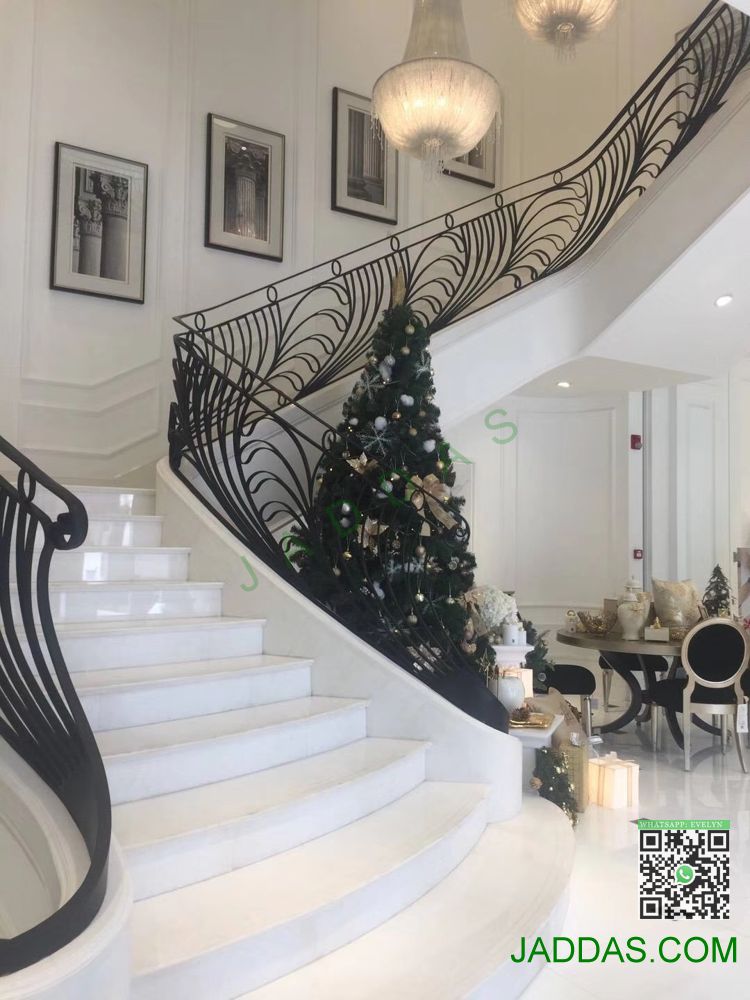
Nano Glass Stair Rise Steps Staircases
A fixing panel on the working table of a hand turning edge cutter shall be used for steel hanging slab edge groove forming, and the slab to be machined shall be clamped vertically; the working table shall be adjusted, and saw blades added or reduced according to machine demand.
Handle finished products with care when depositing them; stack them vertically and do not stack too many at once to avoid damaging slabs.